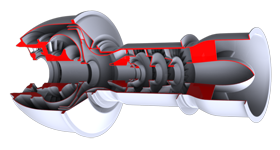
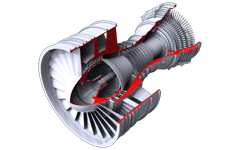
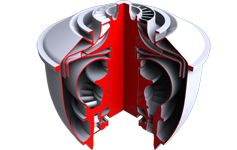
Dynamic analysis of non-straight rotors
The current trends in aerospace industry towards more flexible rotors operating at super-critical speeds require accurate modeling of the inertial coupling between flexible bladed disks and shafts or modal interaction effects, for instance. The fidelity of the results can be significantly degraded by the presence of parametric uncertainties in the rotor geometry due to manufacturing. One important issue arising during the design is the quantification of the effects of stacked disks misalignment on the system global flexural behavior. Traditional approaches through equivalent "rotor-bow" or "unbalance" forces applied to nominal system lead to significant underestimation of the vibration response. This motivates modeling of misalignment phenomena as parameter-dependent perturbation to system matrices. To facilitate the analysis with rotor continuum 3D FE formulation, it is essential to have accurate low-order models that are significantly faster to solve to examine possible combination of the uncertain parameters at various operating conditions.
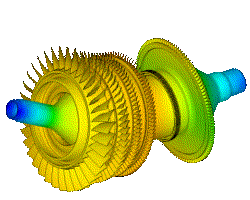

Dynamics of mistuned bladed-disk assemblies
The blade-to-blade structural property variations in bladed disk assemblies are practically unavoidable due to the random nature of manufacturing processes or in-service wear. This problem is commonly referred to as "mistuning". It has a dramatic effect on the vibration behavior of a bladed-disk system. It may lead to spatial localization of vibration energy around a limited number of blades and increase the amplitudes and stresses of blades compared to perfectly tuned system. Those computationally efficient algorithms that analyze exactly periodic structures using the theory of cyclic symmetry fail to accurately predict the dynamics of a disordered system. This motivates the development of reduced-order models that are of sufficiently low order to calculate the response efficiently during MC runs and possess reasonable accuracy. A method that combines the computational efficiency of small mistuning Component Mode Synthesis with the accuracy of the Static Mode Compensation allows to study the effect of "large mistuning" superimposed with realistic "small mistuning".
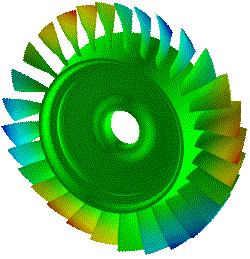
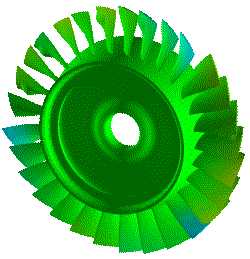
Intentional mistuning and shape optimization of multi-stage bladed rotors
The scope of this research activity is twofold:
- The first topic concerns the modeling of mistuned multi-stage bladed rotors and their dynamical analysis. Of particular interest is the introduction of intentional mistuning for the control of flutter instabilities. A potential strategy is to combine two recent advances in this topic: the multi-stage cyclic symmetry method and the component mode mistuning method.
- The second topic concerns the shape optimization of multistage bladed disks in order to enhance the dynamical behavior of the rotor and minimizing its mass, for instance. Optimization parameters are the geometric characteristics of the disk only and optimization criteria are the modal situation and fatigue endurance among others.


Abradable coating modeling
Abradable coatings are now frequently used in turbomachines in order to reduce potential damages due to direct unilateral contact bet- ween structural components. This research project aims at developing an accurate modeling of abradable coating removal. Numerical simulations of experimental set-ups are conducted to calibrate model's parameters. The solution method considers one-dimensional plastic elements. Simulations are carried out with time-marching explicit integrators. Centrifugal stiffening is also accounted for.
Results feature wear maps which represent the abradable profile around the casing. A color code indicates the wear level from no abra- dable removed in dark blue to severe removal in dark red. Critical speeds are detected for large vibratory amplitude of the blades. These critical velocities are sensitive to various parameters such as:
- material properties of the abradable liner
- blade design
- type of contact initiation
- blade/casing clearance configuration
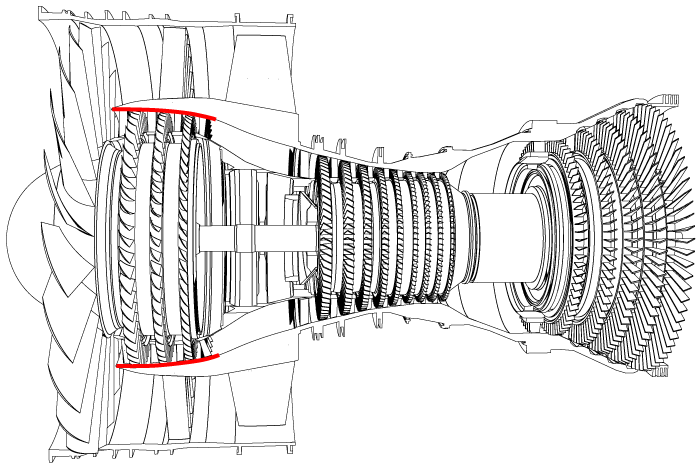
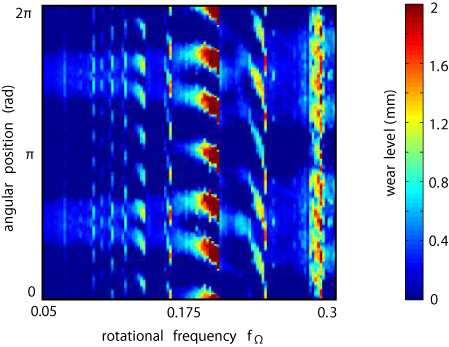
Unilateral contact and friction in aircraft and helicopter engines
In rotordynamics, nonlinear coupling forces between the rotating and surrounding stationary parts can result in unexpected significant amplitudes of displacement and subsequent high stresses. Several different mechanisms can originate such a rotor-to-stator interaction and are usually classified in three main categories:
- interacting forces due to variations of fluid pressure without structural contact,
- interacting forces reduced to a unique contacting point along the circumference of both structures,
- interacting forces induced by multiple simultaneous contacting points at different locations along the circumference.
From a structural point-of-view, the first two categories are decently well understood. The third category is an emerging field of research since higher energy efficiency is achieved by reducing this tip clearance. An undesired consequence is the possibility of rub between the components. Depending on the nature of the induced contact, theses interactions shall force the mode shapes with subsequent high stress levels within the structures. Several numerical tools involving structural models with increasing degrees of complexity are being developed in the laboratory.


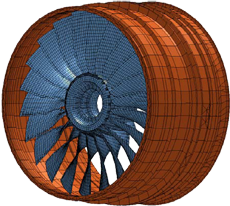
Radial compressors in helicopter engine have also shown interactions during operation that resulted in structural damages. Related sophisticated geometries are numerically challenging and feature higher stiffness than common axial blisks. Attention is paid to modal resonances where stationary casing and rotor modeshapes geometrically match at certain engine speeds. It is intended to improve the design process by eliminating dangerous interactions.
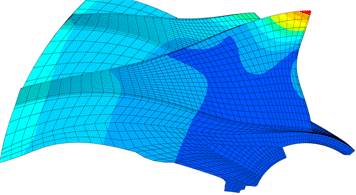
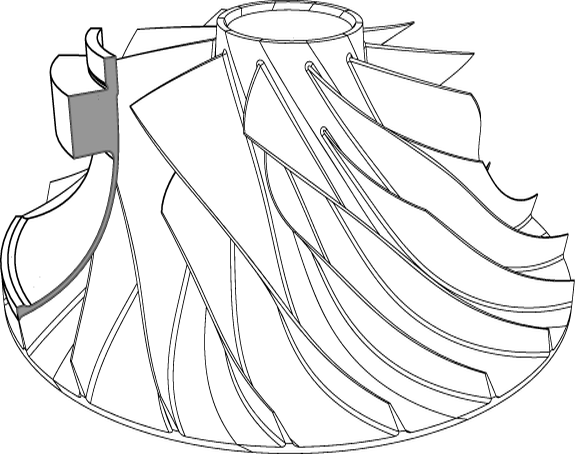
Delay differential equations for wear modeling
Delay Differential Equations (DDEs) have proved to be very suitable for the modeling of the cutter-workpiece interaction phenomena in various manufacturing processes such as milling and turning. To some extent, this interaction may be compared with blade/casing contact in aircraft engines where abradable coatings are implemented as sacrificial materials in order to minimize operating clearances. Consequently, blade/abradable coating contact events lead to abradable removal without damaging the blade. A better understanding of the subsequent interaction calls for more qualitative modelings. This work targets the DDE framework.
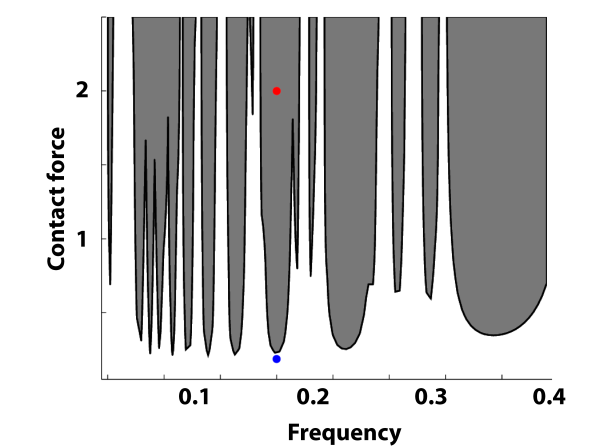
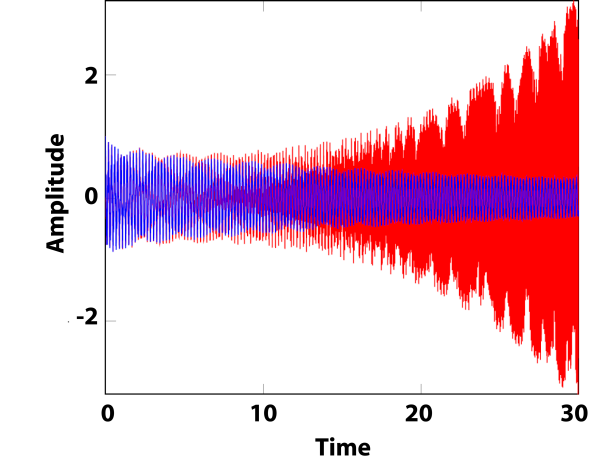
Modal analysis of nonlinear systems
Non-linear modal analysis is now considered as a valuable and efficient tool for the dynamics analysis of non-linear mechanical systems. Related issues were investigated in the past decades among which:
- methods of analysis (analytical/numerical)
- reduced-order models
- stability and bifurcations of solutions
Currently, a major challenge is to consider non-smooth non-linearities in large-scale mechanical systems in the framework of non-linear modes. As an example of research in the lab, the animation below displays modal characteristics of a turbine blade with contact at its tip edge:
- the evolution of the eigen-frequency, manifold and mode shapes in function of modal amplitude is shown,
- the stiffening effect of unilateral contact on the frequency of vibration which changes when modal amplitude increases is obvious.
This highlights the potential risk of failure due to stress concentration caused by contacts. Modal analysis appears as a useful and predictive tool in design processes.

Complex structures with localized nonlinearities
The aim of this research is to find efficient and practical ways of modeling non-linear vibration by exploiting the fact that non-linearities often occur in localized regions of the structure. Examples include: brake systems with a local non-linear frictional contact; oil-well drills with localized interactions with the borehole wall; mooring lines with non-linear fluid interaction close to the ocean surface where large displacements occur; turbine blades in contact with their casing structure; growing fatigue cracks with locally varying stiffness as the crack opens and closes; frictional interaction between the bow and string of a violin; and any structure with a joint will introduce some degree of non-linearity at the interface.
Such systems present a modeling opportunity: efficient linear methods can still be used to describe the majority of the structure so that the computational effort is focused on the small regions of non-linearity. Recent developments in linear analysis and uncertainty modeling will be combined with non-linear methods, and model development will be closely tied to experimental validation. The project is based in the Dynamics and Vibration Research Group at Cambridge University Engineering Department and is being carried out in collaboration with the Structural Dynamics and Vibration Laboratory at McGill University.
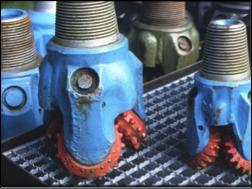
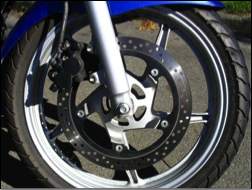